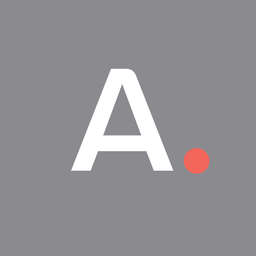
Article
Hi, let's find you a remote job!
about 1 month ago
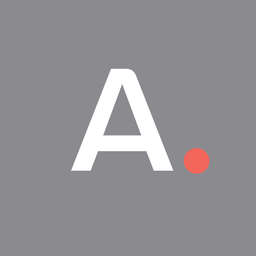
Hi there, we’re Article. 👋 We’re a North American based furniture company creating remarkably better furniture experiences one sofa at a time. And as the Vendor Quality Specialist – Outdoor Furniture , you will conduct Factory Quality Audits (QMS) of vendors, develop quality standards, train stakeholders on quality requirements, work on corrective actions, and provide support for escalated issues within the Outdoor product category, conduct the pre-shipment inspection, in-house testing etc.
Why We Need You:
As the Vendor Quality Specialist – Outdoor Furniture, you will ensure the consistent delivery of high-quality products to our customers. In this role, you’ll lead factory audits, conduct inspections, manage vendor quality performance, and support continuous improvement initiatives across our outdoor furniture supply chain. Your expertise will help strengthen vendor accountability, elevate product standards, and drive cross-functional collaboration to uphold Article’s commitment to exceptional quality.
Why Article?
While we sell to the North American market, we work closely with a number of our manufacturing partners throughout Asia. As a result we have an office in Thao Dien, Ho Chi Minh City, Vietnam where we currently have around 60 Particles (people of Article) working.
As a Particle (people of Article), you will have a high level of autonomy to solve challenging, meaningful problems in the best way you can. That means you’re trusted to explore solutions you believe will work best (you’re the expert, after all). You’ll do all this while growing your skills within a company that is redefining the furniture industry.
What You’ll Do:
- Report to the Vendor Quality Lead within your dedicated product category to strictly adhere to the determined quality process and improve the product quality performance.
- Conduct factory quality audits (FQA) to evaluate quality management systems and production capabilities of vendors.
- Conduct Pre-shipment inspection for newly launched products and products identified with a high-quality focus.
- Participating and giving quality inputs in the Pre-Production Meeting (PPM) for New Product Introduction (NPI).
- Receiving claim tickets (Jarvis) from the customer care team and categorizing them into the correct category (manufacturing defects, packaging/transportation, or appeasement).
- Supporting Quality Claim Analyst to have technical/quality dialogue with vendors for pending / unresolved claims.
- Conduct an Inline inspection for products identified with high quality focus.
- Based on product issues or vendor trends, work on projects with relevant stakeholders to continuously improve the product quality (reduce defect rate) through effective implementation of the Corrective Action Plan (CAP).
- Participating in establishing internal quality processes, templates, and inspection quality standards.
- Prepare a monthly quality report for vendors who are under your responsibility and organize a quality meeting to address the issues.
- Participating in establishing or updating test standards.
- Supporting to conduct of on-site in-house test for NPI.
- Follow up the validity of the golden sample/color swatches.
- Administer the quality records, including the validation and uploading of PSI report, Inline inspection report, FQA report, CAPA reports, etc..
- Develop training materials for in-person and online training, and update documentation when quality standards or requirements change.
- Train vendors and internal stakeholders on quality requirements and framework.
- Provide technical support to sourcing and product development teams when structural issues or quality issues are identified on samples or on launched products.
- Visit vendors as required to review samples, assess production capabilities, and quality systems.
- Conduct analysis on quality issues and testing failures to identify and implement preventative measures, including but not limited to assessing testing standard requirements.
- Monitor the quality performance on a monthly basic and evaluate quality processes in the field, and identify opportunities for improvement.
- Collaborate on cross-functional projects with internal stakeholders, including Operations, Product Engineering, Sourcing, Planning, and Ocean.
- Excellence on quality skills/tools like 7 QC tools, SPC, FMEA, 6 Sigma etc.
Perks & Benefits:
Life:
- 15 vacation
- 11 National Holidays & 1 extra day for Christmas
- 6 well-being (sick) days
- 1 Inclusion and Diversity Day
Health:
- Excellent extended health care benefits packages (dental, health check, mental health…)
Company & Office Space:
- State-of-the-art laptops with the tech and tools to easily collaborate
- Be a part of a dynamic company and an internationally recognized brand